Device Optimization
Based on the automation and computerization application projects of the Vietnam National Coal - Mineral Industries Group (TKV), the period up to 2025, with a vision to 2030, Dak Nong Aluminum Company has deployed a series of technological solutions to modernize production activities.
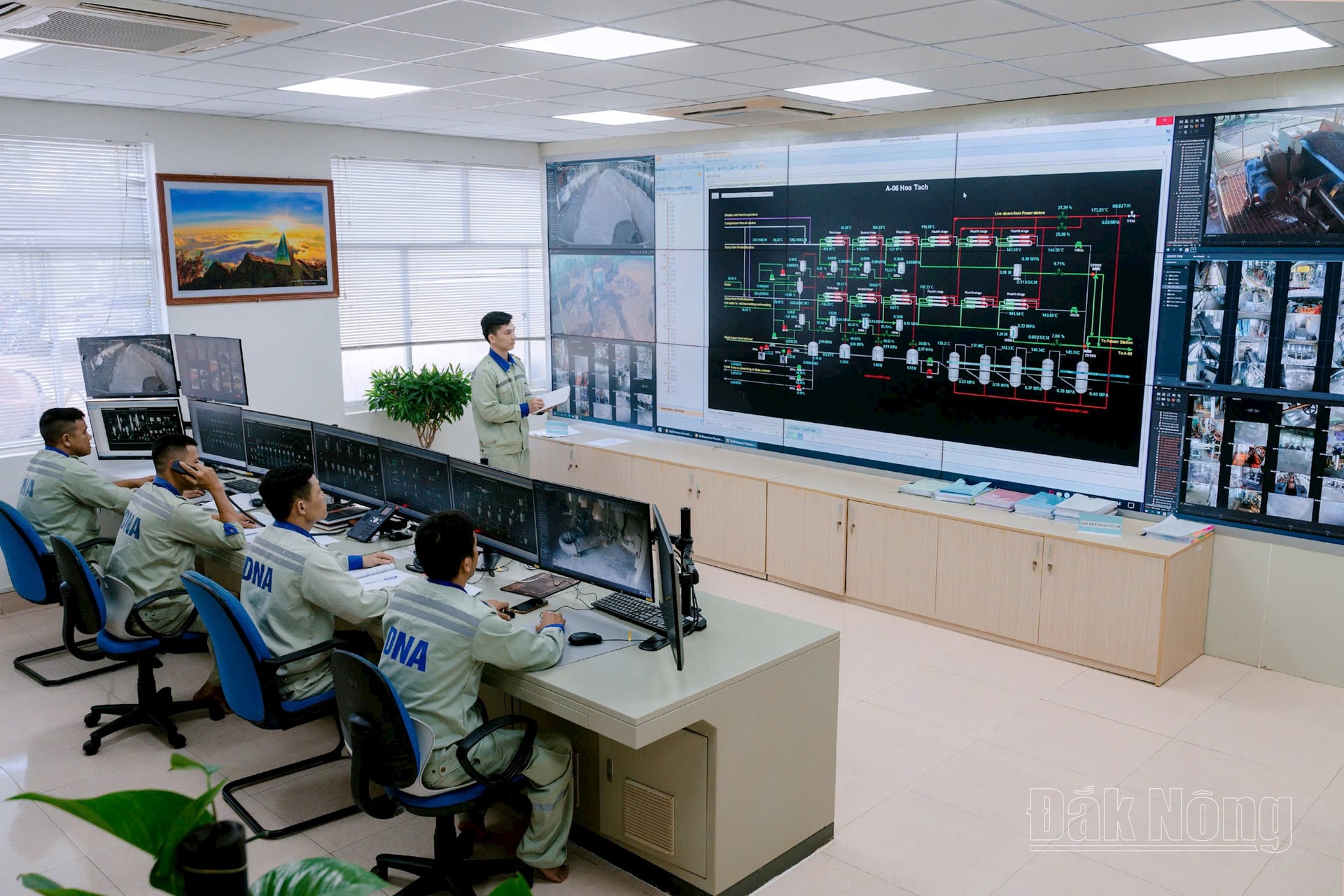
Specifically, regarding the application of automation, the company has repaired and upgraded the control system in workshops such as: coal gasification, hydrate burning, thermal power...
At the same time, automate some areas and equipment such as: boilers No. 1 and No. 2 of the thermal power plant, 12 gas generators of the coal gasification plant, and automate the hydrate furnace.
Transfer some monitoring stations that control auxiliary areas to centralized control and monitoring at the central control room of the areas...
The control system at the Production Control Center was repaired and upgraded to achieve overall consistency, ensuring synchronization between control systems in areas within the factory. This helps prepare for the phase of connecting centralized control of the entire complex at the center.
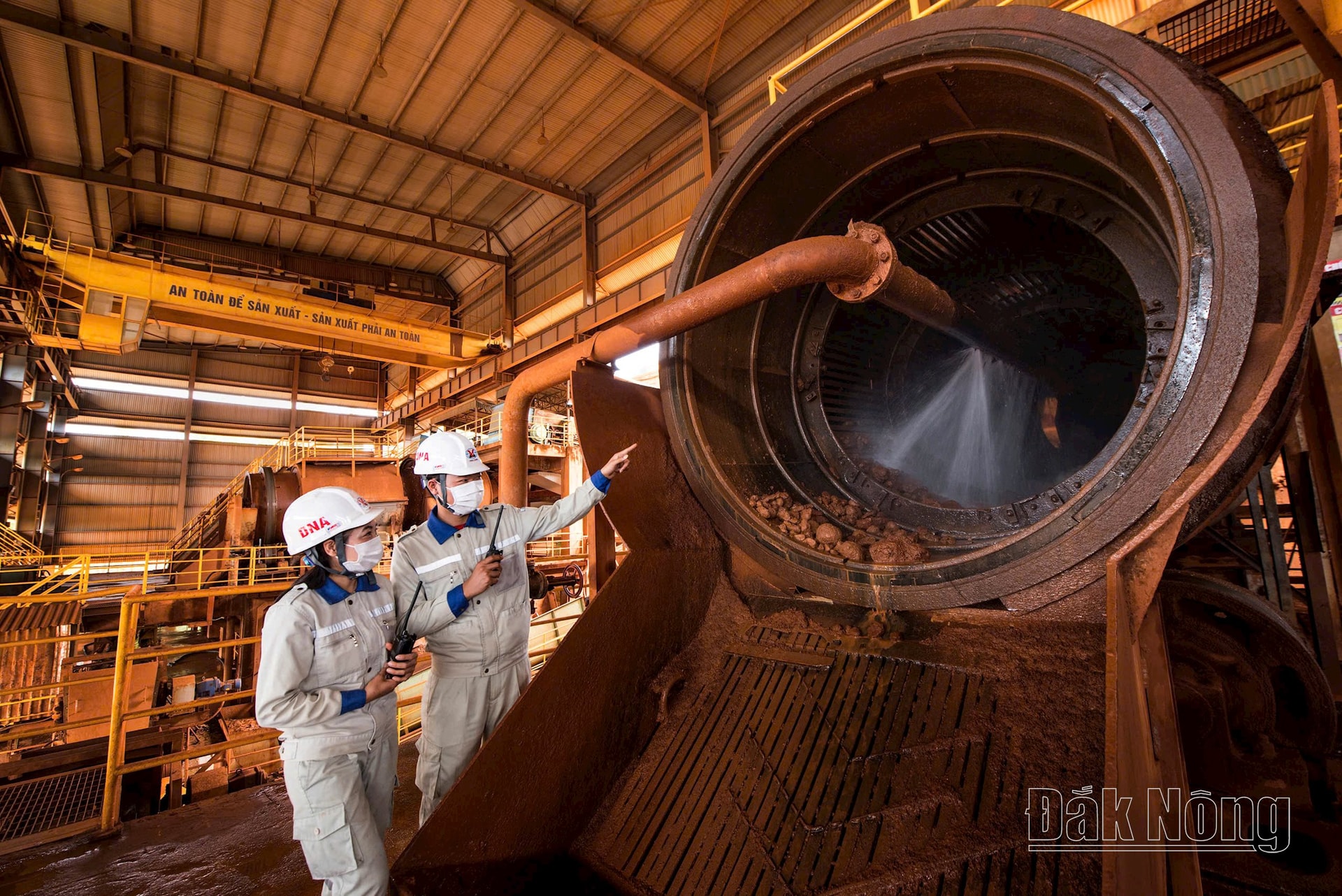
The company also repairs and upgrades network infrastructure, adds storage devices, shares data connectivity, and enhances security and network safety for the system.
Hexagon EAM software in electromechanical management and integrated electronic inspection function is applied to all electromechanical equipment in the production line complex on mobile application.
The company also applies software for shift handover and production statistics; applies software for managing document archiving; upgrades electronic office software and applies digital signatures...
The above applications have contributed to the successful implementation of the company's production and business plan and laid the foundation for development in the following years.
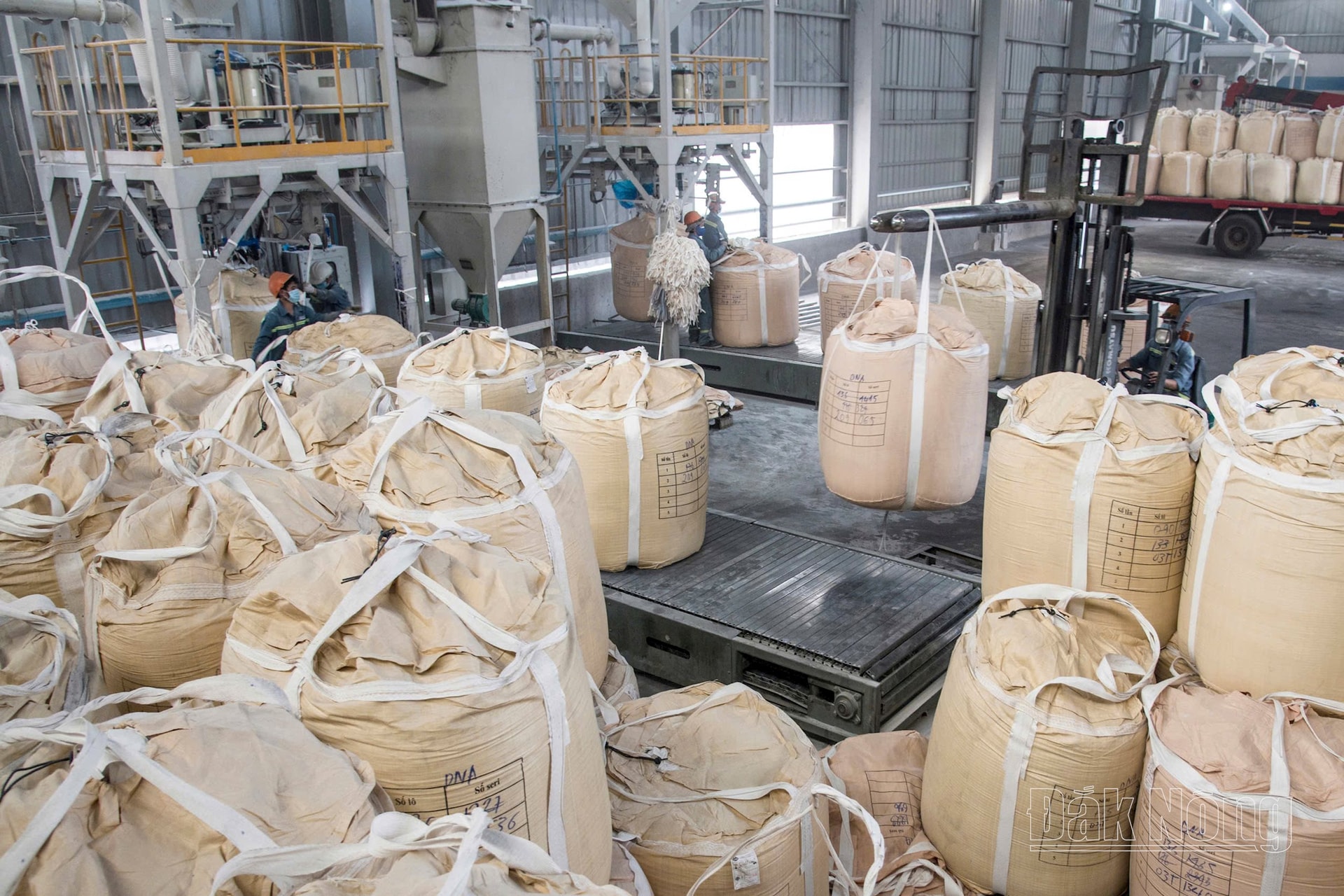
This is also an important factor in helping to reduce direct labor, increase labor productivity, increase safety levels, and optimize the operation of equipment in production stages.
Mr. Nguyen Tien Manh, Deputy General Director of TKV, emphasized that in the coming time, Dak Nong Aluminum Company needs to focus on optimizing the production process and effectively using existing resources.
At the same time, TKV promotes creativity, technical innovation and production rationalization to increase productivity, ensure product quality and reduce production costs.
Automation is key
Nhan Co Alumina Factory Project is one of the key projects, with modern technology, built and put into use in the era of rapid and extensive development of the 4.0 industrial revolution.
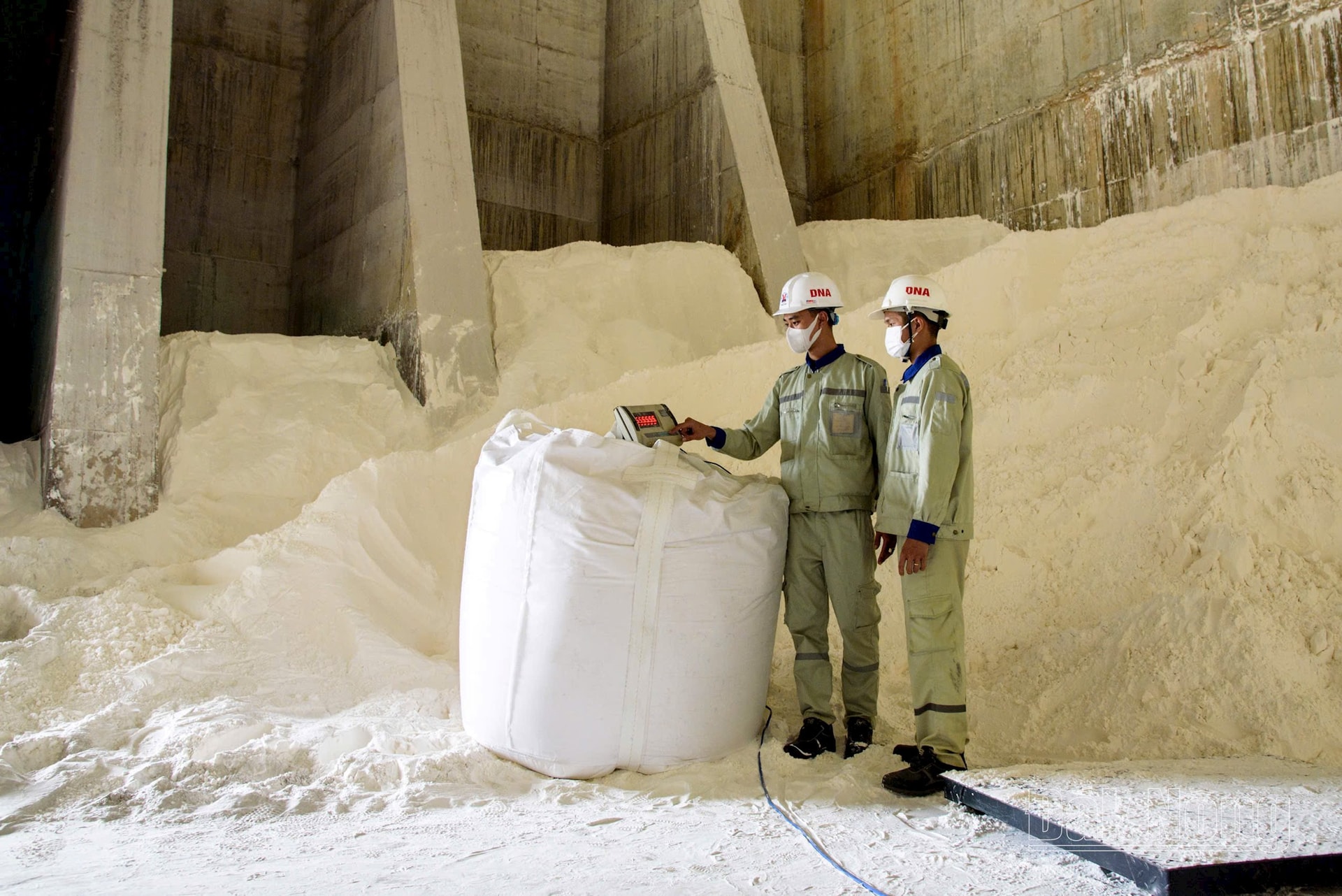
Along with maximizing the exploitation of the existing IT infrastructure and automation system, the company is upgrading and adding new technology suitable for the times to modernize alumina exploitation and processing, reduce product costs, and compete according to market mechanisms.
The company is aiming for a digital enterprise by 2030. In particular, it focuses on developing digital infrastructure to serve activities in a centralized and consistent manner, helping to improve management capacity and labor productivity.
The unit identifies urgent tasks, priority levels and ensures consistency with TKV's orientation and policies on digital transformation and automation.
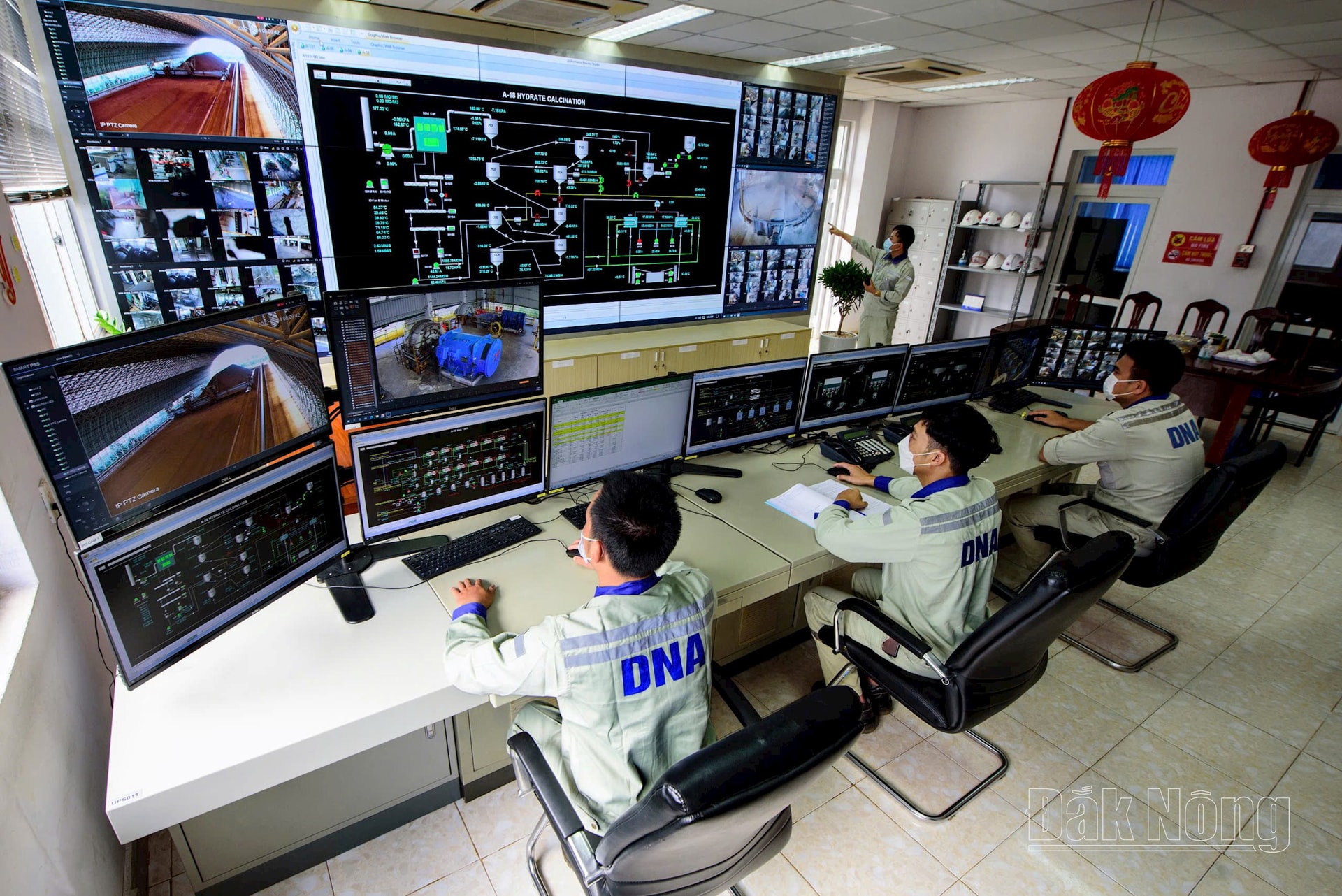
The company is currently completing digital transformation platforms such as: technical economic norms system; operating procedures; regulations on technical management, electromechanical, economic management, cost and material management; connecting infrastructure platforms...
From there, standardize and digitize data to serve the digital transformation task later.
During the implementation process, the unit always ensures the connectivity and ability to inherit data, integrating software solutions closely and synchronously. Thereby, ensuring the connection between existing software and new investment software through the data integration axis.
This also helps to form a synchronized digital transformation ecosystem within the entire company. This is also the main goal to help reduce investment costs and improve efficiency in deploying technology solutions.
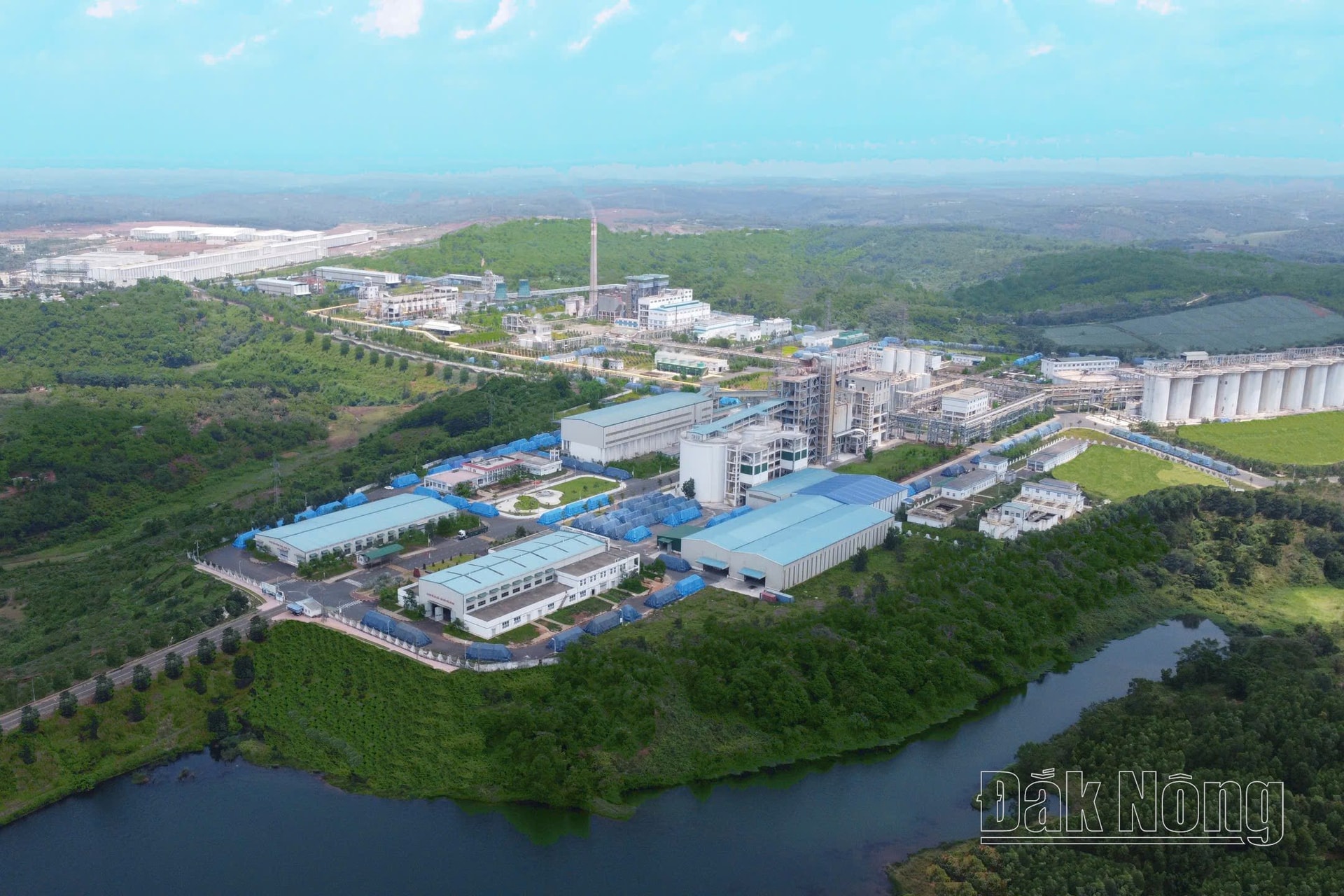
The company is continuing to build synchronous SCADA/DCS control systems, applying intelligent production management systems with the ability to comprehensively integrate data from rooms and workshops.
Modern measuring devices, actuators and advanced control algorithm applications are being replaced by the research unit to automate the production line complex of Nhan Co Alumina Factory.
This helps to optimize production processes, improve equipment monitoring efficiency, predict failures and improve supply chain management, support accurate decision making, reduce operating costs, improve product quality and ensure factory sustainability in the new era.
Source: https://baodaknong.vn/cong-ty-nhom-dak-nong-va-no-luc-toi-uu-hoa-cong-nghe-trong-hoat-dong-247206.html
Comment (0)